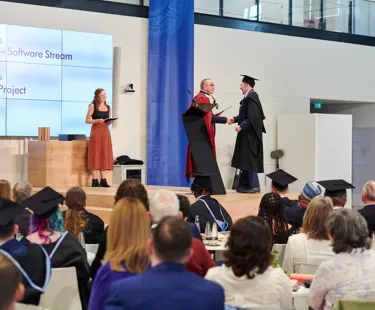
Dyson Institute Alumni files patent for Dyson
We spoke with Dyson Institute Graduate and Dyson Engineer Guy Turner, to hear about his work in the New Software team at Dyson, and the power of Software Engineering.
Guy Turner is a recent graduate of the Dyson Institute program, joining the Institute in 2019. Since graduating, Guy is now working for Dyson as a Design and Development Engineer in Dyson’s London NPI Lab, alongside further Postgraduate studies. Guy worked on software innovation and strategy for future products, he supported product development from concept to manufacture, and worked on the de-risking of emerging technologies. He has a strong passion for engineering, Design and Innovation, with 4+ years of experience with Dyson in the UK and Singapore.
Currently Guy is a Postgraduate Innovation Design Engineering (IDE) double masters student at Imperial College and the Royal College of Art (MSc and MA) and is a recipient of the prestigious Industrial Design Studentship from the Royal Commission for the Exhibition of 1851.
So, you’ve been able to file a patent through your work at Dyson, that’s a great achievement, which team were you working in?
"As part of my two-year placement during the Dyson Degree program, I worked in the NPI Software Team in Bristol. This team focuses on exploring emerging technologies and de-risking new features across all of Dyson’s product categories. I was based in the Embedded Software team led by David Halls. I worked across many projects across the two years, from future Environmental Care concepts, Floorcare, Wearables, and Air Quality research."
What was the project that led you to this piece of work?
"I had the opportunity to be involved in a piece of research exploring new methods to estimate the filter lifetime of our Environmental Care products. These devices act as a fan whilst simultaneously purifying the air inside your home. Over time, the filters inside capture pollutants and eventually become completely saturated, needing replacement. Making sure our customers know when to swap them accurately is crucial, so we can both minimise the environmental impact and cost to customers, whilst ensuring their purifier is always capable of effectively purifying the air they breathe as it’s designed to do.
I supported research into a novel way to estimate the remaining life of our filters more accurately than ever before, using advanced software techniques and Machine Learning. This removed the need for additional parts, which could have increased the cost of the product and increased manufacturing impact to the environment. It’s important to consider how one small change to a product that is sold globally in the millions of units can have a significant impact.
Supporting the Environmental Care Research Team and Machine Learning teams, I led the development of a prototype Dyson Purifier. The prototype had an onboard Linux computer collecting diagnostic data from the internal motor and an array of environmental and pressure sensors, these research prototypes were cloud-connected. I also developed software to allow us to remotely monitor these sensors and analyse data in real-time.
A dozen were built in total and sent home with Dyson engineers as part of a home trial. Over many months, we collected various data sets to learn about the correlation between the motor and onboard sensors behaviour against the pollutants captured by our filter. From this data, the Machine Learning team were able to develop an edge machine learning algorithm which can be run on the device to predict the remaining filter lifetime."
That's an interesting piece of work, and it sounds like it could have strong impact on future products, what did you do to take the work from an idea, through to something more concrete?
"This project spanned 6 months of development, from design to software development and electronics prototyping. This was followed by the home trial which ran for another 6 months. Many teams were involved in this work and supported along the way, Dyson has some of the world’s leading researchers and I was very privileged to work with them at this stage in my early career."
What did you enjoy the most about this project?
"This work was a highlight of my time at Dyson – working collaboratively with many different engineering and scientific disciplines, coming together to develop work that is not only novel and interesting academically, but also has significant potential to improve our products globally. A project that can make our products better at purifying, but also improve the sustainability of our filters is a huge win for customers, Dyson, and the planet."
How did the Dyson Institute help you or make your feel confident doing this work?
"I specialised in Electronics Software and learnt about Software development, Data science, Machine learning, Internet of Things, and Connectivity from my lecturers. Being able to put this knowledge into practice within the workplace was exciting, and showed how relevant it is to solving real-world problems."