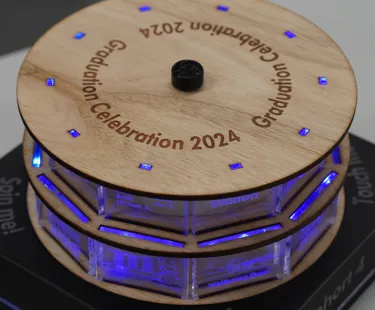
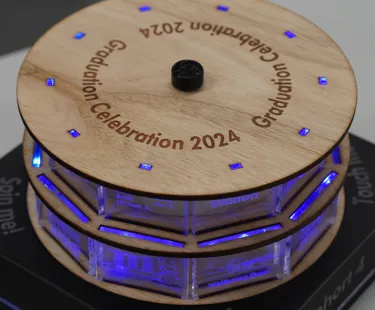
An emerging tradition across the Dyson Institute graduation celebrations is the student-designed table centrepieces. These are displayed at the events dinner, which is held in the Lightning Café on the Dyson Malmesbury Campus. The original design was created by our first cohort in 2021, it featured a laser engraved acrylic top, a wooden base with RGB lights connected by WiFi so all 40 centrepieces change colours in sync. Each year has made incremental improvements to the design, including changing the construction, new light designs.
This year's centrepieces feature a complete visual redesign, with a new shape inspired by the Roundhouse, and windows etched with moments and key places over the past four years.
We spoke to the 2024 design team to get their insights into the process, and how they got the incredible final result.
Why did you want to tackle this project?
Kuba Rogozinski – I enjoy prototyping electronics and software so when the opportunity to work on the centrepiece appeared I was intrigued, having seen the previous centrepiece designs I thought there were some improvements we could make
Luke Pike – I wanted to give this a go because I love everybody in the cohort and love making souvenirs so thought it would be cool to make a unique souvenir for everyone.
Aidan Plant – I wanted to get involved in making our graduation stand out from the others by taking the centrepiece to the next level and making it encompass our time at the Institute.
How were you inspired by the previous year designs?
Luke – The engravings from last year and the uplighting they had was really cool, that and the WiFi connectivity so we can coordinate all the lights remotely.
Kuba – The previous iterations were a good foundation when it came to software as the lights control program and hardware used worked well and was easy to work with for modifications (Thanks James BP), the physical construction and design were something we wanted to overhaul entirely. Being a rectangular centrepiece with a thin acrylic pane as the focal point it means that anyone say directly parallel to it would see nothing but its cross-section. Therefore, Aidan suggested we make a 360-degree centrepiece inspired by the Roundhouse building to make it accessible to everyone around the circular table.
What have you added this year?
Kuba – We've added a lot of features, mainly from an interactivity point of view, the roundhouse can freely rotate such that the main body can be examined at all angles, this is important as each window of the roundhouse is etched in a similar way to previous designs, but this time rather than 1 picture there are 20, each related to a place, experience or memory we believed was important to us during the course. Additionally, the light control system has been upgraded so that it is not only controllable via the internet, but also on the centrepiece itself. This means it is easier to control at home after the event, but also adds an element of fun during the dinner as there is a possibility to sync up the centrepieces such that when one person changes theirs by touching it, it will propagate to everyone.
The last change which is something entirely new is a QR code on the centrepiece which contains links to important information relating to the day such as the dinner menu, but also graduation photos and a custom-made poster by myself, showing all the components and assembly required to put it together.
What were some of the challenges you faced this year?
Aidan – Co-ordinating such a large group (7 people) during one of the busiest periods of our studies was difficult. Once Final Year Project and End Point Assessment were completed we all had much more time to focus on the project. We had issues with having the top half lit well while keeping all the electronics in the non-moving base, having components in both pieces would have got wires tangled up and been a mess! Construction has also been a challenge, the sheer number of components and the complexity of some parts was daunting.
Kuba - There are a few, but off the top of my head it would have to be the LED strip, the product is circular, and the LED strip is, well... a strip, so it doesn’t coil up nicely to form a circle. We opted to cut the LED strip to make a pentagon of 5 strips to better fit the circular design but that introduced a lot of soldering work, over 1100 solder joints alone for the LEDs across all of 40 centrepieces. Then scaling up the acrylic etched panels from 1 to 20 meant a lot of components. Each centrepiece has 31 components prototyped in house specifically for it. At a scale of 43 units totals that over 1300 components to assemble.
We almost had a proper production line going on at one point with people soldering, peeling acrylic from all the windows, gluing and assembling at the same time which is a testament to how much more complex this design is compared to the past; however, the result is well worth it in my opinion.
What makes projects like these interesting?
Kuba – I think it's the freedom of making something that doesn’t have to comply with the same regulations like we do in our normal work. Here we own the project and want to make something that will ultimately be used at our graduation, and we will take home so it’s got to look cool!
Luke – The project would always be fun because it is designing and making stuff. The feeling of getting a functioning prototype back and assembling is amazing.
Aidan – The open ended nature meant that we could do whatever we wanted and we let our imagination run wild… before reigning it in a bit to make sure we end up with something viable!
How would you like to see this project evolve next year and beyond? Is there anything you wish you could have tackled this year?
Kuba – One thing that everyone has been telling me as I’ve been showcasing it: “Why does it not spin on its own?” or “Why is there no motor?” Try adding that if you fancy it...
Luke – Next year? I’d probably say a model of the village with different lights that cycled based on the kitchens.
Aidan – I think next year they should create something different and make it unique to their cohort like we did this year. Although I wish we had made the bearings smoother and given it some cool under glow.